The Role of LRTM in Lightweight Automotive Parts

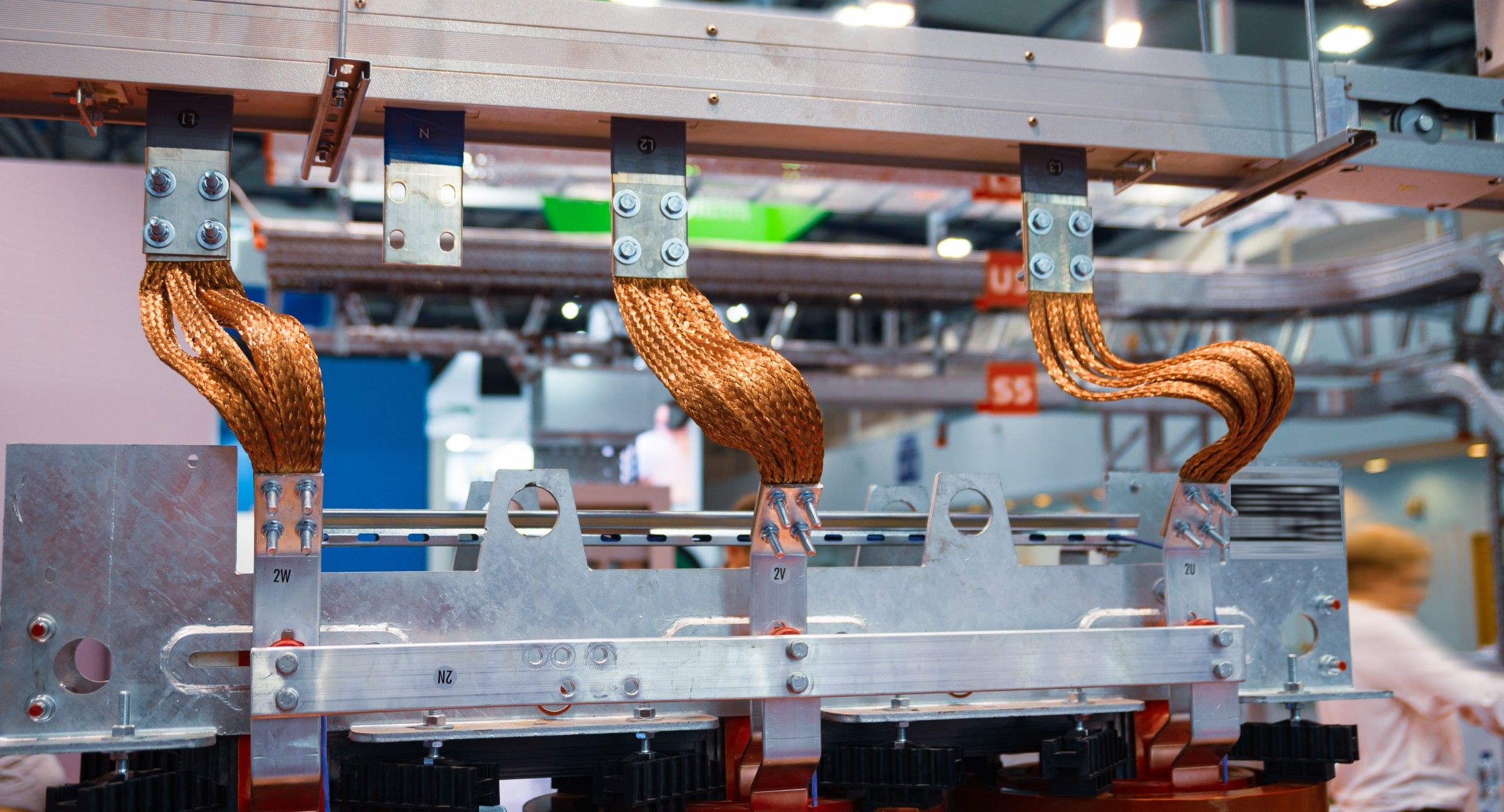
The automotive industry needs parts that are heavy-duty yet lightweight and cost-efficient yet precise. That’s a tall order, and unfortunately, traditional manufacturing methods often fail to deliver.
Luckily, light resin transfer molding (LRTM) offers a superior alternative. Here’s why more industry leaders are making the switch to LRTM for automotive applications.
What Is Light Resin Transfer Molding?
If you’re new to the process, think of the LRTM process like you would a waffle maker that sandwiches batter between a top and bottom mold to create an even waffle with consistent patterns.
Unlike single-sided tooling, which only molds one surface (leaving the other exposed for manual finishing), LRTM gives you a finished product that is identical on both sides.
The LRTM process begins by placing fiberglass inside both halves of the mold. The mold is then sealed and injected with resin under low pressure to:
- Ensure even distribution
- Eliminate air bubbles
- Create consistent finishes that look identical on both sides of the mold
The material then cures under controlled temperature and pressure, transforming the liquid resin into a solid material.
LRTM For Automotive: The Benefits
Lightweight Yet Durable
The automotive industry is under intense pressure to reduce vehicle weight to meet fuel efficiency standards. The LRTM process is ideal for creating lighter parts without compromising strength and safety.
Superior Finish
With traditional manufacturing, products often come out of the mold with defects—they’re rough, uneven, and contain visible fiber patterns or air bubbles. To get rid of these defects, manufacturers must sand, finish, and paint the parts, which means increased labor costs.
The LRTM process bypasses this altogether, as pieces come out of the mold with a smooth, defect-free finish. No additional processing required.
Faster Cycle Times
On the front end, the low-pressure process can be slower than traditional manufacturing methods. After injecting the resin, we use low pressure to help create even distribution and less fiber displacement. However, by ensuring precision from the outset, we actually save time in the long run by eliminating post-processing.
Versatility
Another benefit of LRTM for automotive use is that it is incredibly versatile. Not only does it allow us to create complex designs with a perfect finish, but it also allows for a range of material options, sizes, and shapes.
What Our LRTM Process Offers the Automotive Industry
25+ Years of Experience
We’ve been in the manufacturing game since 1997 and have used the LRTM process to produce a range of premier automotive parts—everything from driver dashes and instrument panels to fender flares, engine doors, and battery trays.
Cross Industry Experience
We have 25+ years of experience in the automotive industry. But we have just as much experience in the medical, marine, industrial, and other sectors. That range of experience gives us a broader range of knowledge about materials and processes. It also allows us to apply innovative solutions from other industries to yours.
From Concept to Completion
Give us your design and specs, and we'll make it—or give us your rough idea, and our team will help you refine it. That's the beauty of working with Painted Rhino. We meet you where you are, no matter what stage of development you're in.
Manufacturing—Your Way
An advantage of working with Painted Rhino is that we offer flexible manufacturing solutions. Whether you need help refining an idea, want to create a prototype, or are ready to begin full-scale production, we can accommodate you.
Driving Innovation Forward
Want to reduce production costs without compromising quality? Painted Rhino can help. Whether you need LRTM for automotive, vacuum and thermoforming, or tooling and metal work, we offer comprehensive services built around your needs and budget. Contact us today!