The Role Of Injection Urethane In Today’s Industrial Applications

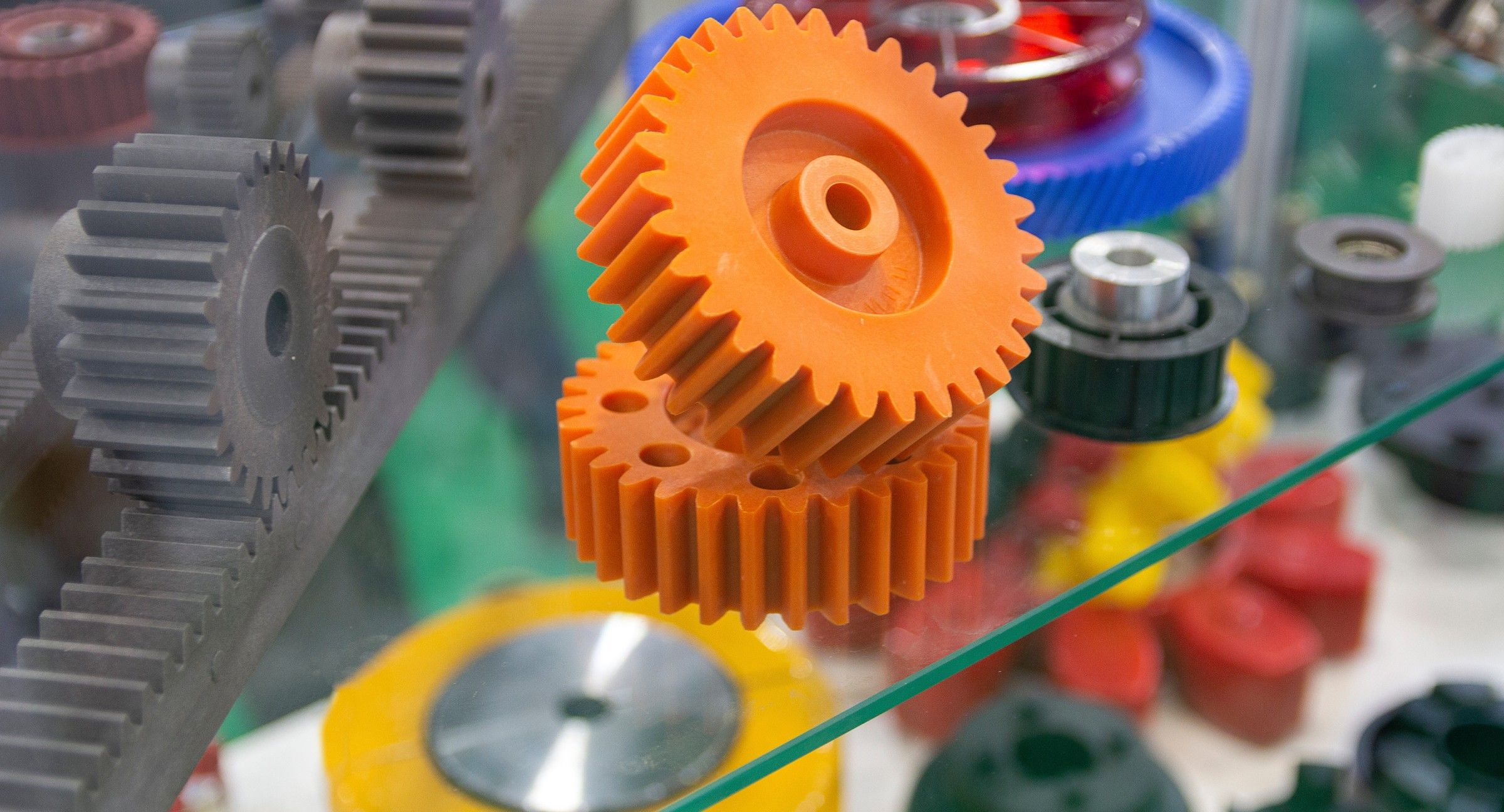
Urethane has a wide range of applications and beneficial properties that make it critical for modern industry. Few alternative materials offer superior results when it comes to the things that injection urethane does well.
There are many reasons to use injection urethane in today’s industries, which is one of the reasons it’s such a common industrial component. Here’s what you need to know:
Industrial Benefits Of Urethane Properties
Any material being put to industrial use needs to be evaluated on its properties, strengths, and weaknesses as compared to similar materials, and its suitability for any given project.
That said, one of the advantages of urethane is that there are several different kinds of urethane with various properties. Urethane also comes in two basic types, hot cure and cold cure, with distinct advantages and disadvantages in practical use.
While hot-cure urethane tends to have superior properties over cold-cure formulations, cold-cure has the advantage of being practical in situations where hot-cure urethane isn’t an option.
Here are some of the fundamental properties associated with injection urethane:
- Hardness: Urethane has a wide range of hardness, from 30 shore A to 75D.
- Wear Resistance: This property is one of the primary benefits of urethane since urethanes tend to have exceptional wear resistance. Abrasion resistance increases with hardness.
- Compressive Strength: Urethane performs well in applications where a high degree of compression resistance is required. Except for urethane foam, urethane is incompressible.
- Tear Strength: In addition to high abrasion resistance, urethanes offer high tear strength and resist tearing even when damaged.
- Tensile Strength: This is a weakness of most urethanes since they tend to elongate and creep rather than resist pull.
- Heat Build-up: Another weakness is that urethane does not perform well as an insulator, especially in dynamic and high-load applications, since urethanes tend to have cascade failures once the internal temperature of the material reaches a certain point. Some urethanes are an exception to this rule, but they tend to be more advanced and more expensive materials than the urethanes used in other applications.
Urethane Casting
One of the most common uses of injection urethane is in urethane casting, where the chemicals needed to create the desired urethane are injected into a mold. The urethane is then allowed to cure and maintain the mold’s specific shape after curing.
Using different forms of urethane can give the cast part other properties. Since urethane takes detail well, molds can be made for various practical applications, with a high level of detail and a high success rate.
Choosing the proper urethane formulation for your needs is critical, as is ensuring that the mold can handle the temperatures needed for hot cure urethane when hot cure urethane is preferred.
As a result, injection urethane has a vital role in industry and manufacturing, both in creating the needed parts for other industrial and manufacturing machines and in creating end-user products that perform well in real-use applications.
Because urethanes have a wide range of physical properties, they are an essential part of an equally wide range of processes and products. Some examples of urethane (also called polyurethane) uses include:
- Prototyping and product design
- Wheels and rollers
- Automotive parts and applications
- Shock absorbers
- Medical devices
- Consumer products
This is an incomplete list but includes some of the most important uses of urethane today.
The Painted Rhino Difference
When you need lightweight and durable parts in large volumes, injection urethane molding and rotocasting are fantastic options, and at Painted Rhino, we’re as committed to your success as you are.
Our team knows manufacturing inside and out with our decades of experience. So get in touch with us to get a quote today!