Creating Durable Molds: Best Practices and Materials

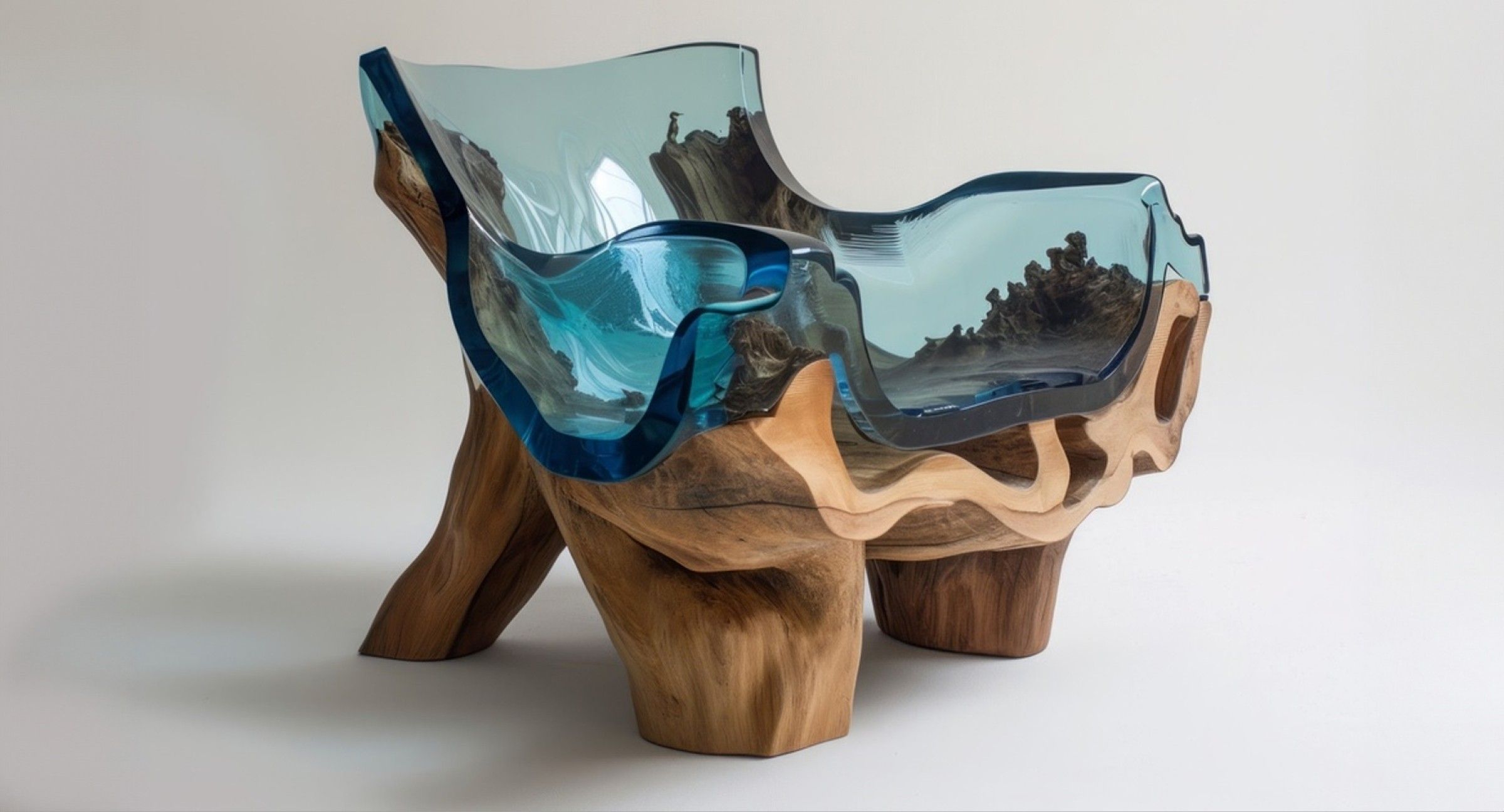
Bringing creative projects to life requires more than a one-size-fits-all approach. This is especially true when it comes to molds, where the choice of material and technique can make or break your final product.
While many fiberglass and composite parts manufacturers only offer limited molding options, we are pleased to offer a variety of techniques that allow us to create detailed, sturdy, and elegant products that perfectly match your project requirements.
Understanding Molds: Why Do Different Projects Require Different Molds?
Every successful fiberglass part begins with choosing the right mold—whether it’s used for injection molding, vacuum-forming, or another manufacturing process. The type of mold we use is often dictated by the project requirements, including:
Surface Quality Needs
While a fiberglass boat hull may need a pristine Class A finish, industrial parts might favor structural integrity over surface appearance. To meet these requirements, our team must select the appropriate mold material and preparation techniques.
Part Complexity
Complex parts with tight corners and intricate details often require carefully engineered molds and manufacturing techniques. Sometimes a project calls for multiple molds to accommodate undercutting. In other instances, a simple one-piece mold is sufficient. It all depends on the project and usage requirements.
Production Volume
How many parts do you need? The answer to that question often dictates the mold. While a temporary mold might be sufficient for a prototype, full-scale production runs typically require durable solutions that maintain quality with repeated use.
Mold Options and Manufacturing Processes
At Painted Rhino, we use a variety of molds in our production processes, including:
Mold Making for Resin
Resin is a versatile material that begins as a liquid and cures into a solid plastic. The material is used to create anything from jewelry and tables to countertops and custom auto parts. Casting resin requires a mold that can withstand heat while ensuring proper curing and easy release to avoid damaging the final product.
Silicon Mold Making
When intricate details matter, we may use a flexible silicone mold. Not only do they capture complex details, but they are also easy to remove, allowing us to create intricate patterns that wouldn’t be possible with traditional molds.
Injection Mold Making
When projects require lightweight yet durable results, we often suggest injection molding. During this process, thermoplastic is injected at high speeds into a mold, creating consistent, high-quality parts in rapid succession. To ensure quality, we use epoxy or aluminum molds that can withstand high pressure and repeated use.
Fiberglass Molding
When it comes to fiberglass, we typically use three processes:
- Hand Lay-Up: The most basic and versatile molding method, hand lay-up is a manual process in which we apply fiberglass and resin layers into the mold. The process takes more time but ensures precision and quality control.
- Chopper Gun: To fulfill higher production orders, we may use a chopper gun that sprays a mixture of chopped fiberglass and resin into the mold. It’s an automated process that allows us to cover more surface area quickly.
- Vacuum-Assisted Resin Transfer Molding: In this process, we use vacuum pressure to draw resin through fiberglass—then seal the mold with a vacuum bag. Why? To remove air bubbles, ensure even distribution, and create a higher fiber-to-resin ratio.
Helping Customers Break the Mold Since 1997
Need help bringing your next project to life? You’re in the right place. At Painted Rhino, we offer numerous manufacturing techniques. Whether you need a prototype, short-run, or large-scale production, our team will bring your project to life using the right techniques and the right molds. Contact us today!